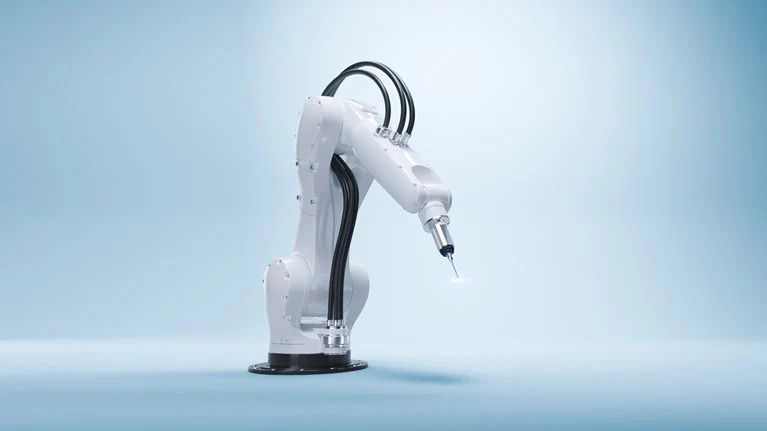
Augmented reality, machine automation, and more: the 21st-century industrial revolution is digital. Industry 4.0, the Fourth Industrial Revolution, and 4IR all refer to the current era of connectivity, advanced analytics, automation, and advanced-manufacturing technology that has been transforming global business for years. This wave of change in the manufacturing sector began in the mid-2010s and holds significant potential for operations and the future of production.
What is the Fourth Industrial Revolution?
Get to know and directly engage with senior McKinsey experts on industry 4.0.
Enno de Boer is a senior partner in McKinsey’s New Jersey office. Kweilin Ellingrud is a senior partner and a director of McKinsey Global Institute in the Minneapolis office. Gérard Richter is a senior partner in the Frankfurt office and leader of McKinsey Digital Hubs and Build by McKinsey in Europe. Daniel Swan is a senior partner in the Stamford, Connecticut, office.
Steam propelled the original Industrial Revolution; electricity powered the second; preliminary automation and machinery engineered the third; and cyberphysical systems—or intelligent computers—are shaping the Fourth Industrial Revolution.
Before 2014, the Google search term “Industry 4.0” was practically nonexistent, but by 2019, 68 percent of respondents to a McKinsey global survey regarded Industry 4.0 as a top strategic priority. Seventy percent said their companies were already piloting or deploying new technology.
4IR builds on the inventions of the Third Industrial Revolution—or digital revolution—which unfolded from the 1950s and to the early 2000s and brought us computers, other kinds of electronics, the Internet, and much more. Industry 4.0 brings these inventions beyond the previous realm of possibility with four foundational types of disruptive technologies (examples below) that can be applied all along the value chain:
- connectivity, data, and computational power: cloud technology, the Internet, blockchain, sensors
- analytics and intelligence: advanced analytics, machine learning, artificial intelligence
- human–machine interaction: virtual reality (VR) and augmented reality (AR), robotics and automation, autonomous guided vehicles
- advanced engineering: additive manufacturing (such as, 3-D printing), renewable energy, nanoparticles
Technology, however, is only half of the Industry 4.0 equation. To thrive in the Fourth Industrial Revolution, companies must ensure that their workers are properly equipped through upskilling and reskilling and then hire new people when necessary. Upskilling means that employees learn new skills to help them in their current positions as the skills they need evolve. Reskilling is the real challenge: workers are retrained with new skills that will enable them to fill different positions within their companies.
This is increasingly vital as disruptive technologies transform job requirements, but the outlook on reskilling differs geographically. In Europe, 94 percent of surveyed executives believe that the balance between hiring and reskilling should be equal or tip toward reskilling, compared with only 62 percent of US respondents.
The end-to-end skill transformation has three phases:
- scout—analyze the skills required to achieve a company’s ambitions
- shape—identify talent gaps that must be addressed and design the program infrastructure to address them
- shift—develop and implement content and delivery mechanisms to train workers at scale
A conversation with Francisco Betti (head of the Platform for Shaping the Future of Advanced Manufacturing and Production, launched by the World Economic Forum in 2017) and the CEOs of Flex, Protolabs, and Western Digital offers perspective and real-world insights on building workforce capabilities and shifting mindsets for successful digital transformations in manufacturing. The benefits can go far beyond business outcomes. In the words of Western Digital CEO David Goeckeler, “It’s not just about our company being better and us being prepared for the future; it’s about all of our employees being ready for that future—keeping them at the center, having them highly engaged, all of the reskilling, getting them excited about what the future holds.”
Learn more about our Operations, Advanced Electronics, Financial Services, Technology, Media & Telecommunications, and Sustainability practices.
What is The Global Lighthouse Network?
The World Economic Forum, in collaboration with McKinsey, launched the Global Lighthouse Network (GLN) in 2018 to identify organizations and technologies in the vanguard of the Fourth Industrial Revolution. A lighthouse (in this context) is a manufacturing site that has successfully implemented 4IR technologies at scale, with a significant operational impact.
Lighthouses aim to capture more than 80 percent of the identified value of chosen use cases—meaning those involving 4IR technologies. Ultimately, these sites are intended to serve as an Industry 4.0 benchmark for the transformation of other sites. This may sound similar to the concept of a digital factory—because it is. Digital factories serve as “construction sites” for companies to implement 4IR technologies and test-run new operations before applying the advances at scale. The difference is that the GLN specifically identifies lighthouses as successful 4IR trailblazers.

Introducing McKinsey Explainers: Direct answers to complex questions
Today, 103 lighthouses—such as Tata Steel’s plant in Kalinganagar, India, and select Henkel Laundry & Home Care production sites—have been identified around the world.
Lighthouses can be built practically anywhere, by small or big companies, in developing or developed economies, and at greenfield or brownfield locations.
Insights from lighthouses that are successfully using 4IR technologies today offer something of a playbook for organizations shaping the future of manufacturing. Digital transformation at scale isn’t easy, but responsible production—combining productivity, sustainability, and active workforce engagement—is within reach.
To get there, six core enablers can boost the odds of success for your company’s 4IR transformation:
- An agile approach that incorporates quick iterations, fast fails, and continuous learning, with teams transforming bundled use cases in waves to drive innovation and ongoing refinements.
- Agile digital studios can help people collaborate effectively, providing designated space where team members from different functions are in proximity for co-creation.
- The IIoT stack allows for seamless integration of IIoT infrastructure (both legacy and new) to build a stable, flexible tech backbone. Costs can by limited by leveraging existing systems with efficient investment in a new technology stack.
- An IIoT academy uses adult-learning best practices to upskill the workforce, offering customized learning programs based on the unique individual needs.
- Tech ecosystems partner with vendors, suppliers, customers, and related industries to source the latest capabilities, offering access to extensive data sets and creating opportunities for innovating together.
- Transformation offices can form a governance hub to support the launch and scale-up of a lighthouse, making progress and priorities transparent, ensuring value continues to be captured, and accelerating change.
Of these, two are particularly important: an agile approach and a transformation office.
Any company can begin its Industry 4.0 journey in a small way at one site and then scale up quickly. Otherwise, it could be doomed to “pilot purgatory”: companies try out (or pilot) new technologies but fail to apply them at scale, stalling the 4IR transition. As of late 2020, about 74 percent of surveyed companies reported being in pilot purgatory.
What are the advantages of the Fourth Industrial Revolution?
The Fourth Industrial Revolution could make products and services more easily accessible and transmissible for businesses, consumers, and stakeholders all along the value chain. Preliminary data indicate that successfully scaling 4IR technology makes supply chains more efficient and working hours more productive, reduces factory waste, and has countless other benefits for employees, stakeholders, and consumers.
Implementing Industry 4.0 technology is also especially advantageous amid the challenges of the pandemic. In fact, COVID-19 has accelerated the 4IR transition because physical distancing and shifting consumer demands forced companies to embrace digitization and contactless operations. Six months into the pandemic, 94 percent of the respondents to a McKinsey survey said that Industry 4.0 had helped keep the operations of their companies running, and 56 percent considered these technologies critical to the crisis response.
Before the pandemic, the top motivators for companies to digitize varied by industry. But in 2020, three drivers were common across all sectors and geographies: agility, flexibility, and manufacturing efficiency. Companies that had already scaled up Industry 4.0 technologies before COVID-19 were better positioned to handle the challenges that arose.
- One consumer-packaged-goods company in Asia built a digital twin of its supply chain to simulate different scenarios. During the pandemic, the company used this simulator to prepare for sudden shutdowns or disruptions in the supply of materials.
- When one coffee machine plant in Treviso, Italy, transformed itself from an uncompetitive site into a manufacturing lighthouse, labor productivity rose by 33 percent and lead times fell by 82 percent.
- Of the surveyed companies that had not begun implementing Industry 4.0 technologies, 56 percent felt constrained in their responses to the pandemic’s challenges as a result.
Learn more about our Operations practice.
Tell me more about the Fourth Industrial Revolution, workforce engagement, and the future of manufacturing?
Workforce engagement is vital to a successful 4IR transformation. Indeed, even a company with the best tools, newest technology, and immense resources is unlikely to scale up a 4IR transformation successfully if the workforce is not engaged. A concerted focus on people has also helped organizations build resilience by helping workers develop new skills, so that the business can respond more flexibly to change. In practice, this could entail rethinking training and skill development pathways, and make structural changes for the longer term.
Here are five areas where manufacturers are already promoting high workforce engagement:
- learning and development (for example, with extended competencies and skills, via the combination of hard, soft and digital skills, and apprenticeship)
- empowerment and ownership (for instance, through outcome and results-oriented steering, or by encouraging workers to make their own decisions)
- collaborations and connections (say, by working with cross-functional and multiskilled teams, or developing extended networks in the organization and beyond)
- impact and recognition (for example, by creating accountability for achievements or by celebrating successes)
- the voice of the worker (for instance, by using digital channels and data to gather input from workers’ voices, or by seeking to understand their hidden needs)
How about Industry 4.0 digitization and opportunities for sustainability?
The Fourth Industrial Revolution creates opportunities for sustainability and, more important, these advances are inherently more sustainable than current business practices. Some people think productive operations are hard to square with environmental responsibility, but sustainable lighthouses challenge that notion: 4IR transformations facilitate a viable kind of eco-efficiency that intrinsically meshes sustainability with competitive excellence.
Eco-efficiency includes three dimensions of digital technology:
- enabling data-informed actions in production and the broader end-to-end value chain
- realizing improvements across performance indicators, such as cost, agility, convenience, and quality
- driving sustainability gains by limiting consumption, resource waste, and emissions
Consider a few examples of how Industry 4.0 technologies that maximize efficiency also minimize waste:
- One Singapore lighthouse decreased its scrap output from building semiconductors by 22 percent in a smart factory enabled by the industrial Internet of Things, or IIoT. (See a related Explainer, “What is the Internet of Things?,” for more.)
- Schneider Electric’s smart factory in Lexington, Kentucky, combined IoT connectivity and predictive analytics to lower energy use by 26 percent, CO2 emissions by 30 percent, and water use by 20 percent.
- Sixty percent of the 103 lighthouses identified by the Global Lighthouse Network include sustainability among their top five Fourth Industrial Revolution use cases.
And more broadly, lighthouses demonstrate how 4IR technologies can promote responsible growth in the long term. How? Through action in three broad areas:
- Environmental: Taking care of our planet and the surrounding environment. Areas of focus for lighthouses in this category include energy, water, waste, greenhouse-gas emissions, and the circular economy.
- Social: Building a stronger workforce and community. For lighthouses, focus areas might include human-capital development, the voice of the worker, health and safety, and labor standards.
- Governance: Establishing a set of practice, controls, and procedures to govern, make decisions, and meet the needs of stakeholders. This can encompass focus areas such as ownership, accountability, business ethics, and governance structure.
Learn more about our Operations, Digital McKinsey, and Sustainability practices.
What is Industry 4.0’s impact on the economy?
Industry 4.0 will continue to have a significant impact on the economy. The greatest economic boons will go to the fastest-acting companies.
According to a 2018 McKinsey Global Institute analysis, Industry 4.0 front-runners—facilities well on their way to adopting AI and other advanced technologies by 2025—can expect a 122 percent positive cash flow change. Follower companies can expect just 10 percent, while companies that wholly fail to adopt AI could see a 23 percent downturn.
Industry 4.0 is also projected to transform the skill sets of the workforce by shifting the standards for sought-after talent. Over the coming decade, we will see these changes as more and more companies embrace robotics:
- Demand for physical and manual skills in repeatable tasks, like those on assembly lines, will decline by nearly 30 percent.
- Demand for basic literacy and numeracy skills will decline by almost 20 percent.
- Demand for technological skills such as coding will rise by more than 50 percent.
- Demand for complex cognitive skills will rise by about 33 percent.
- Demand for high-level social and emotional skills will rise by more than 30 percent.
In 2025, the value creation potential of Industry 4.0 for manufacturers and suppliers is expected to reach $3.7 trillion.
What industries are being transformed by Industry 4.0?
Every single industry will be transformed during the Fourth Industrial Revolution, but some to a greater degree than others. The nature of the Industry 4.0 transition will differ by the specific types of technology being adopted, as well as the existing infrastructure and skills of organizations. The transformation can be broken down into three archetypes of adoption pathways:
- Accelerated. Regardless of a company’s existing tech infrastructure (whether advanced or nonexistent) certain inexpensive digital, augmented-reality, and automation solutions are rapidly adoptable without transition headaches.
- Differential. The existing tech infrastructure will affect how quickly some technologies are adopted. Companies with less foundational information technology (IT), operations technology, and data infrastructure will need time to transition. More advanced companies are better equipped for quick implementation.
- Slowed or deferred. Even at companies with an advanced tech infrastructure, the adoption of the most cutting-edge innovations (such as full end-to-end automation) will be slow because of the high level of required capital expenditure and the unclear long-term payback.
Operationally intensive sectors, such as manufacturing, transportation, and retailing, will experience the greatest change because many companies in these sectors employ large numbers of people for tasks particularly suited for automation or digitization. Operations-intensive sectors have 1.3 times more automation potential than others do.
In these operations-intensive sectors, McKinsey analysis indicates that up to 58 percent of work activities could be automated with current technology. Education, by contrast, is projected to undergo the least degree of change during Industry 4.0; only 25 percent of the sector’s work is automatable.
Learn more about our Operations practice.
For more in-depth exploration of these topics, see McKinsey’s collection of insights on operations. Learn more about manufacturing and supply chain consulting, and check out manufacturing-related job opportunities if you’re interested in working at McKinsey.
Articles referenced include:
- “CEO dialogue: Perspectives on productivity and sustainability,” November 3, 2021, Enno de Boer, Yves Giraud, and Daniel Swan
- “Lighthouses unlock sustainability through 4IR technologies,” September 27, 2021, Francisco Betti, Enno de Boer, and Yves Giraud
- “A manufacturer’s guide to scaling industrial IoT,” February 5, 2021, Andreas Behrendt, Enno de Boer, Tarek Kasah, Bodo Koerber, Niko Mohr, and Gérard Richter
- “Building the vital skills for the future of work in operations,” August 7, 2020, Kweilin Ellingrud, Rahul Gupta, and Julian Salguero
- “Industry 4.0: Reimagining manufacturing operations after COVID-19,” July 29, 2020, Mayank Agrawal, Karel Eloot, Matteo Mancini, and Alpesh Patel
- “Lighthouses reveal a playbook for responsible industry transformation,” March 30, 2022, Francisco Betti, Enno de Boer, and Yves Giraud
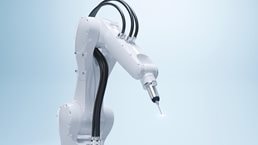