In recent years, companies in high-hazard industries have made great strides in responding to safety hazards. The trouble is, these hazards seldom come to light unless an incident occurs. However, new technologies are now giving companies a reliable way to measure employees’ ability to detect potential hazards in their working environment. This enables organizations to design interactive programs to improve their safety performance and culture.
Consider a hissing valve emitting steam, a missing handrail on a high platform, or a pool of black oil on a white-tiled floor. Such hazards pose a threat, but they are plain to see, and the danger they represent is obvious. They are not the problem.
Think instead about a sharp metal edge at head height just behind you, a pressure gauge tipping past the operating limit, or an isolation valve closed but not locked, with a bar handle at kick height. These hazards could be lethal, and if your people don’t see them or recognize the danger they pose, that is the problem.
In a recent visit to an offshore oil rig, we spotted a sign warning employees about high noise levels from machinery temporarily sited in a quiet area. The trouble was, the sign was so close to the machinery that anyone able to read it would already be at risk of hearing impairment. Ironically, the presence of the warning sign didn’t reduce the hazard but magnified it.
In our work supporting companies with their large-scale safety transformations, we’ve found that the biggest obstacles to maintaining a consistently safe workplace are the employees’ ability to see and predict hazards and the leaders’ under-standing of that ability. The good news is that both obstacles can be tackled with the aid of new tech-based approaches.
Improving hazard awareness
Oil and gas companies have made strenuous efforts to improve safety performance in recent years. Between 2014 and 2017, personal safety in the industry improved by 15 percent per year, and process safety improved by 7 percent.1 More recently, though, personal safety showed no improvement, and process safety declined in the period from 2017 to 2018.
Many companies refer to a “safety staircase,” like the one illustrated in Exhibit 1, to describe the cultural changes they are pursuing to improve their safety performance. However, leaders often struggle to categorize their organizations accurately. A company that considers itself proactive, for instance, may find that field visits and team interviews uncover lingering signs of a calculative approach—such as an awareness among leaders of how many safety observations have been conducted compared with targets but a failure to dig into the issues revealed by these observations. Such signs suggest that the company would need to make major changes if it were to move to a generative culture, in which safety observations are quickly used to make safe working easier through modifications in workers’ behaviors and the streamlining of procedures.
Through our work with companies seeking to climb up the safety staircase, we’ve found that leaders need to set the right tone and expectations for teams’ safety behaviors, create an environment that motivates people to look for and speak up about hazards, and provide systems for acting promptly when a hazard is identified. But powerful as these leadership actions can be, their effectiveness ultimately depends on the individual employee’s ability to see hazards and recognize them as such. This ability varies considerably from one individual, site, or company to another; it may not be well understood in the organization; and it is likely to show considerable scope for improvement.
One oil and gas operating company had experienced several safety incidents involving dropped objects at one of its sites. When leaders visited other sites, they discovered that field teams and supervisors were still overlooking similar types of hazards, and as a result, no effort was being made to control them. Instead, the company’s safety-awareness program focused on energy isolation and improving compliance with personal protective equipment. Although these topics were important, they didn’t represent the most immediate risk to employees’ safety.
Would you like to learn more about our Oil & Gas Practice?
The company realized that what it was looking for (the hazards it was hunting) didn’t correspond to what was happening on the ground (the kinds of incidents that occurred at its sites), and it was limited or distorted by what people could see (their hazard awareness). This insight enabled the company to refocus its employees on the reality of their working environment and coach them to see and control genuine hazards. As a result, physical risks became visible before they went on to cause safety incidents and were handled preemptively through new systems and behaviors, enabling the company to take employee engagement and safety performance to a new level.
The main challenge in improving hazard awareness is the lack of a reliable, quick method of measuring it. Much of the hazard-detecting ability that exists in teams is earned at a high cost from investigations into previous incidents, direct personal experience of accidents, or near misses. This is a reactive, slow, partial, and painful way to learn. But better alternatives are now available.
Using virtual-reality tools
Leading oil and gas companies are pioneering an immersive new approach to safety awareness that combines training with assessment, and is applicable in other high-hazard and labor-intensive industries. The approach uses virtual-reality (VR) tools to expose users to a realistic but hazard-laden work environment like that illustrated in Exhibit 2. As they navigate through the environment, the VR system tracks what they do, taking hundreds of measurements per second. It registers where people look (not just at an object but also above, beneath, or beyond it), how long they look for, whether they detect something, which hazards they find, which hazards they miss, and which “hazards” are in fact benign.
Having tracked each user’s behavior, the tool processes the data using advanced analytics and correlates the output with the individual’s experience, training, and role. The result is a quantitative score that reflects the individual’s perceptiveness in scanning for and identifying different types of safety hazards (Exhibit 3). The performance of teams and departments can also be compared with training and awareness efforts, and the organization’s overall ability to detect hazard types can be compared with the types of incidents and near misses that it experiences.
The assessment process is quick, safe, realistic, and enjoyable to complete. It offers a more reliable and objective alternative to existing methods, which tend to rely on inferring safety awareness after an incident or near miss, assuming it from prior training, or assessing it from interviews or observation. The assessment acts as the foundation for a physical-safety program that helps transform the way people see, identify, and preemptively manage safety hazards. It can also be used to identify employees who need tailored training and coaching.
As part of broader cultural change, leaders should also review how they set standards and inspire their teams to meet them. For example, safety meetings often begin with a review of a specific incident, but that incident may have occurred in another organization, and its relevance may not be obvious. Instead, leaders could ask those attending the meeting to spend 30 seconds reflecting on a recent site visit: What did they do, what did they learn, and why is the site safer now than it was before they visited?
This kind of approach shrinks the gap between talking about safety and getting personally involved and being genuinely helpful. It guides leaders to be fully present at their sites so that they can see hazards, assess how far frontline staff recognize them, and consider what help teams need to control them. It also helps companies unearth hazard blind spots at every level of their organization.
Why virtual reality?
In “real reality” environments, it’s impossible to assess the capabilities of large numbers of workers in a short time. Measuring and improving hazard awareness at scale has long been a stumbling block for safety initiatives, given the limitations of traditional methods. Classroom training sessions can cover thousands of participants in a year, but they aren’t immersive and can’t measure spatial awareness (for instance, did someone look behind them?) in fine detail. Facility walk-throughs are immersive and realistic, but they can’t be done cost effectively with thousands of workers in multiple environments.
With VR applications, hazard awareness can be measured quantitatively, cost effectively, and at scale. Once a management team is equipped with these measurements, it can make data-driven decisions about safety initiatives and monitor their effect over time. This turns backward-looking learning—such as lessons from a worker dropping a tool from a scaffold—into forward-looking control. When pipework is being repaired, for instance, a manager could run through the location of isolation valves, remind the team to lock them to prevent accidental energy release, and ensure they are tested in advance to make certain they hold the pressure for longer than the repair will take to complete.
An organization can run thousands of participants through a VR process within days, benchmark their collective performance, analyze individual performance, tailor training to personal needs, and measure the effectiveness of any capability development completed since the last VR run-through. One petrochemical company completed VR assessments for 700 employees in just three days and was able to review the results with the teams within a couple of weeks.
Nurturing healthy unease and psychological safety
Best-practice organizations know that safety is good for business. They work on two sets of conditions to achieve transparency, build capability, and boost safety performance.
First, they recognize that hazards must be sought out and detected early, while they are still small and haven’t yet erupted into incidents. To help build a hazard-hunting culture, the organization nurtures conscious risk awareness or “healthy unease” in its people. This rests on two factors: the willingness to look for hazards, waste, and opportunities, no matter how safe things appear to be on the surface, and the ability to see hazards, waste, and opportunities, regardless of any improvements that the organization has achieved.
When approached in the right way, healthy unease is an energizing state to inhabit. People never stop looking for hazards and better ways to do things. They constantly unearth flaws in the condition of equipment or the design and execution of tasks, ensuring that hazards are brought to the surface before they accumulate into accidents.
Second, best-practice organizations create a culture of psychological safety. Employees feel not only compelled to speak up about hazards and opportunities but also supported in dealing with them. Sustaining such a culture requires easy-to-use reporting processes and systems for sharing observations on hazards, waste, and opportunities without delay, along with the organizational capacity and will to respond quickly to them. That could mean offering open-door access to leaders who regularly walk the front line, for instance, or introducing dashboards to track hazard resolution visually.
Adopting a blended-learning approach
Companies seeking a step change in safety performance typically follow an approach that combines classroom training, forums, field-based coaching, and peer-to-peer sharing (for instance, visiting sites to observe how other teams work and discuss insights with them). We’ve found this approach effective in developing hazard awareness, prompting behavioral change and building new routines to help transform safety throughout the organization. One oil and gas company ran regular peer calls in which senior site managers and business leaders discussed how they had applied new techniques from training forums in their day-to-day work.
One element of a blended approach is an immersive forum in which leaders internalize the essence of running a safe and high-performing business and then express it in their own words. In one recent program, safety leaders with decades of experience learned how to tell a personal story about “why safety matters to me” to create a deeper connection with their teams. Thanks to these stories, frontline workers who had never raised safety concerns before began offering suggestions to leaders, who promptly acted on them.
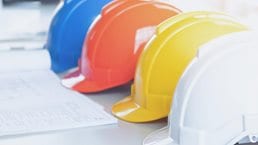
Overcoming limiting mind-sets to improve safety
Another element in a blended approach is practical learning designed to change people’s mind-sets and drive safety-conscious behaviors. It’s often helpful to use “moments of influence”—such as routine prejob safety briefings and plant walk-arounds—to reset processes that have become formulaic and stale through repetition. Moments of influence can also occur in “upset conditions,” or out-of-the-ordinary incidents, such as a leader’s response to safety issues. One oil and gas operating company guided leaders to rethink the way they received bad news. After they began to request and welcome reports of unsafe actions and conditions—and partner with their teams to resolve these issues promptly—the number of preemptive hazard observations multiplied eightfold in three months. Each observation may have prevented an incident that might have occurred had the hazard gone unreported.
Finally, field coaching and peer-to-peer sharing help employees build new safety muscles and moves. In plant walk-arounds, for instance, we found that bringing in an experienced coach prompted even the most seasoned leaders to ask frontline teams deeper questions. This, in turn, triggered new ideas, such as how to optimize the placement of tools and equipment during tasks.
A properly conducted blended-learning approach touches everyone in a given environment. Safety observations increase in quality and number, the organization responds to them more quickly and effectively, and both safety and business outcomes improve over time.
In a recent transformation at a company seeking to achieve a generative safety culture, one operating unit attained six times as many reports of unsafe acts and behaviors and a 55 percent reduction in safety incidents over a six-month period compared with a unit that did not participate in the program.
How to tell if your safety transformation is working
If your company is undergoing a safety transformation, you can be confident you’re making progress if you see certain signs:
- The organization knows what’s happening in its physical businesses in real time across all levels. Unsafe conditions and activities are detected, reported, and acted upon without delay.
- The organization maintains control, even when things change in planned or unplanned ways. For instance, if equipment starts to malfunction, it is immediately checked, the problem documented, and a decision taken whether to suspend operations or continue for the moment with additional precautions in place.
- The organization relentlessly digs deeper into hidden causes, smaller hazards, unseen opportunities, and systematic controls. For instance, it monitors changing trends in the nature and severity of unsafe acts or conditions and the range and number of people who report them.
An organization that has reached this stage in its safety transformation isn’t taken by surprise by hazards erupting into incidents or near misses. Nor does it wait for others to identify hidden opportunities to raise performance. Instead, it hunts for hazards, waste, and opportunities; rapidly captures the benefits to improve the way it does things in the future; and uses what it has learned to uncover the next set of hazards, waste, and opportunities. This virtuous cycle generates continuous improvements in the organization’s performance, safety, and capabilities and takes it closer to the practices and values that characterize the generative stage in safety leadership (Exhibit 4).
Enhancing people’s ability to see physical hazards is the first step in developing the skills and behaviors to control risk. VR tools can help companies understand what hazards people see, extend and deepen these perceptions, and develop fact-based strategies and actions to preempt incidents. A VR assessment can be done in less time than it takes to read a safety flash at the beginning of a shift—and for less money than it costs to buy a pair of overalls. Organizations that make the investment stand a better chance of reducing incidents and demonstrating that safety is good for business.