No one would deny that safety in the workplace is critically important. Most large industrial companies that face workplace hazards devote considerable resources to reducing injuries and incidents. They have a health, safety, and environment (HSE) management system in place and commonly include HSE incidents in annual reports. Yet safety performance at many organizations plateaus after an initial phase of improvement.
Stay current on your favorite topics
This plateau often occurs because organizations attempting to shape safety culture put too much emphasis on tools and processes and pay insufficient attention to the underlying employee mind-sets that shape personal-safety behaviors and interactions.
In our experience, five mind-sets are particularly pervasive in organizations that struggle to improve their safety outcomes. By identifying these mind-sets and harnessing approaches to overcome them, companies can achieve rapid, sustained change.
Five limiting mind-sets
1. Fear of blame: “If I report an incident, I’ll be punished”
At a large transportation company, more than 60 percent of surveyed employees expressed concern about the consequences of reporting an injury. Upon joining field teams, new employees learn both from peers and supervisors the difference between a “true injury” and a “bruise”: the former should be reported and the latter should not. The message is clear—regardless of what these employees learned in their training sessions, it is best not to report too many incidents.
This scenario is all too common in organizations today. In attempts to keep employees from getting hurt, management establishes safety rules and sanctions for breaching them. However, one of the unintended consequences of doing so is that employees may end up underreporting noteworthy incidents for fear of being penalized. When incidents aren’t reported, management and workers lose the opportunity to learn from near misses and low-severity events.
In our experience, two actions can help reverse this mind-set. First, involving the workforce in determining how infractions are treated can help employees perceive penalties as appropriate. Second, and even more critical, is to create an environment in which employees are immediately rewarded or recognized for making safe behaviors and reporting incidents or near misses. This environment encourages reporting and gets people talking about not only unsafe acts to avoid but also desired behaviors.
Take, for example, a North American metal-making plant where safety performance was poor and employee engagement had reached an all-time low. The management team developed an intervention to break the entrenched culture of not stopping to ask for help in potentially risky situations. They gave out metallic tokens inscribed with the company logo to employees who voiced their concerns and sought assistance when they felt unsafe. At the end of their shifts, recipients could deposit the tokens into various bins marked with local charities, and the company would make a $5 contribution to the charity for each token. After a while, employees took such pride in the tokens that they started putting $5 bills in the bins so they could keep the tokens.
2. Disempowerment: “Safety is someone else’s job”
At an Asian chemicals manufacturer, hand injuries accounted for about 50 percent of all serious injuries. When the management team arranged for operators to wear protective gloves, the number of hand injuries declined only slightly. It turned out that many operators decided not to wear the gloves because they made it difficult to perform some tasks. When operators told their field managers the gloves made the work difficult, managers abdicated their responsibility to HSE specialists, who had made the rules. The managers said that these rules simply had to be followed.
In organizations that struggle to improve their safety performance, the lack of employee empowerment is often omnipresent. It’s apparent in leaders who say that if employees followed the rules, they wouldn’t get injured; in team members who claim that incident rates would decrease if management invested in new equipment; and in safety specialists who complain that no one listens to their advice.
To increase employee empowerment, organizations can take a “managed safety” (as opposed to “regulated safety”) approach. That is, management can trust employees to use their own judgment in instances when strict compliance with safety rules either wouldn’t be enough to ensure safety or could introduce risk. This approach is most important in environments with significant variations in operational conditions, which is often the case in industrial settings. To overcome disempowerment, it is also important for leaders to provide positive feedback to teams that take it upon themselves to improve safety.
Would you like to learn more about our People & Organizational Performance Practice?
But while root-cause investigations often reinforce the notion that safety is “in the hands of employees,” organizations must also consider management’s role in safety. In many organizations, these investigations end after leadership establishes that the employee made the wrong decision. Stopping short in this way allows management to feel there is little they could have done to prevent the incident, even though it is their job to ensure people are empowered to follow the rules. More thorough investigations consider potential factors behind the bad decision, such as fatigue or distraction. An even better approach takes a broader look at causes of injuries and incidents to identify structural levers that managers can use to make better decisions.
For example, an industrial company recently used advanced analytics to pull together data sources outside its HSE system, including data on production, human resources, and weather, to identify the primary factors that contribute to employee safety. Roughly 80 percent of the factors that were found to be statistically significant were neither measured nor accounted for in the company’s original investigation methodology. All factors were actually under the control of management—for example, shift duration and training frequency.
3. Trade-off: “Safe means less productive”
An operator at a steel plant was adding alloys to a molten metal ladle. He was asked, “How do you know you’re doing it right?” The operator replied, “It depends. I have a metallurgic procedure in the blue binder and a safety procedure in the gray binder.” The operator, however, was using neither.
This example illustrates that safety and productivity are often perceived as antagonists. Most employees come to work to “get things done” and feel satisfied when they hit their targets. Unless management signals that safety is the priority, employees may conclude that it is acceptable to focus on productivity at the expense of safety.
One obvious way to combat this issue is for leaders to develop clear safety standards that take existing processes into account while integrating safety and productivity requirements. When these dueling processes aren’t integrated, employees can sometimes end up juggling incompatible requirements as they try to do their work, as in the case of the two binders. The failure to integrate these elements can also damage cross-functional relationships. HSE specialists, for example, may feel frustrated by how little influence they have over the operating teams, while operations managers may feel frustrated by the HSE function’s lack of appreciation for the difficulties they face.
In the case of the two binders, a continuous-improvement team conducted a workshop with operators, metallurgists, and HSE specialists to develop a standard procedure, which was then displayed in an easy-to-follow format close to the work station. The improvements to safety and productivity were apparent, with weekly output up more than 50 percent.
A plastics plant in Asia provides another useful example. A plant manager who had just joined the company banned a process for cleaning a critical heat exchanger after seeing how hazardous it was. Operators complained this rule would hurt productivity, which was indeed the case. Convinced that safety and productivity were not incompatible, the manager convened a cross-functional team to solve the problem. The result: a safer, faster, and cheaper cleaning procedure.
4. Fatalism: “Injuries are part of the job”
A review of a European basic-materials manufacturer’s safety culture revealed that the company had a high tolerance for risk. Some operators said that 100 percent safety was impossible and that risk was part of the job. A maintenance operator explained that he sustained cuts and bruises on the job regularly but didn’t report them because he considered them normal.
In focus groups for new employees at another industrial company, workers said they were shocked at the wide gap between what they learned in orientation and what happened in the field. Other employees had come to accept this discrepancy, telling the new employees to “forget the safety stuff you learned in the classroom, or we’ll never get anything done out here.”
This learned tolerance to risk has to do with the pervasive belief that some risks can’t be mitigated. This mind-set is common—even in organizations where managers claim to have signed up for “zero safety incidents.” These managers often haven’t made the effort to understand the implications of aiming for zero. For example, a provider of operations services set everyone’s injury target to zero as part of its annual goal-setting process. But managers did not put enough effort into spreading the idea that the company could achieve such an ambitious goal. People therefore believed this goal was unachievable, so they gave up on it and focused their efforts elsewhere.
Through our fieldwork and research, we’ve found organizations that make progress in eliminating this limiting mind-set work to align leadership and employees on what it means to have a zero goal. In doing so, they collaboratively calibrate expectations to this aspiration. For example, a metals producer, having adopted a zero goal, set stretch but achievable targets for injury reduction and expanded the set of HSE metrics to include positive, leading indicators such as the number and quality of field interactions. With the right context established, people committed to the goals and generally exceeded them.
5. Complacency: “Cultural change takes time”
Many managers assume it takes years for a culture to change. Even those managers committed to change often have low expectations about the pace of improvement, while the uncommitted engage in passive resistance—they wait things out. In either case, the results are the same: a failure to enlist key influencers, generate momentum, and deliver the early wins critical for successful transformations.
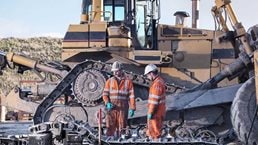
The symbiotic relationship between organizational health and safety
A change in perspective can have a big impact. For instance, a manager who has just had to inform a family that a loved one died in a work-related accident is likely to start talking about safety with a greater sense of urgency. However, managers can’t and shouldn’t wait for this kind of event to find personal meaning. Managers should work to find their own reason for why safety is important to them, and it’s this perspective that would make them an effective promoter of change.
One chemical producer sold off a factory that ranked lowest in safety, productivity, and financial performance because it believed that the plant’s culture was irreparable. The new factory owner shut the plant down for three weeks to revamp operating processes, improve plant tidiness, fix high-priority safety defects, and provide much-needed training. Three months later, the factory had significantly improved its profitability and injuries were virtually nonexistent. The speed and magnitude of the turnaround in performance and culture were remarkable, and it was driven by leaders whose every decision and word communicated an unwavering commitment to the safety and well-being of all involved with the business.
Four methods for shifting mind-sets
Identifying limiting mind-sets is a crucial first step toward building a sustainable safety culture. But to truly effect change in critical employee behaviors, companies need to take a second step: orchestrate a series of mind-set shifts. Four key actions are critical in successfully making this shift.
- Reward safe behaviors. Organizations should encourage desired behaviors by providing positive reinforcement. When it comes to safety, companies tend to naturally focus on reacting to negative outcomes: accidents that happen and people who fail to follow the rules or make safe decisions. This focus is largely because positive outcomes are actually the absence of incidents—or when processes go as planned. Taking this action, then, can be counterintuitive and requires an intentional push from leaders. If management uses reinforcing mechanisms to keep emphasizing a new behavior, mind-sets will shift accordingly over time.
- Clarify that safety is the priority. It’s critical to explain to all employees what is expected of them and why. For example, for an organization to have a positive safety culture, leaders must be explicit about there being no acceptable trade-offs between safety and productivity. Safety is paramount at the expense of productivity. That said, when safety is truly prioritized, productivity often follows accordingly.
- Develop soft skills. While everyone needs to be trained in technical skills, they also need to have the right level of soft skills. Managers need to learn how to both identify systemic issues and provide an environment in which people can speak freely. Operators need to be able to identify hazards and control risk, as well as contribute to a positive, caring team environment. Self-awareness is also a critical soft skill, allowing people to recognize their behaviors and make a shift.
- Role model behaviors from the top. No amount of frontline intervention will make up for a lack of support from top leadership and other individuals throughout the organization who, because of their expertise or personality, have the power to influence behaviors. Employee mind-sets often reflect those of their leaders and influencers because role modeling, whether good or bad, eventually shapes a corporate culture. CEOs who start meetings by acknowledging how the company has performed against its safety goals since the last meeting send the right message about their commitment to safety.
Companies have a multitude of methods at their disposal for improving workplace safety. But building a deeply embedded safety culture by identifying and overcoming limiting mind-sets is key for improving safety outcomes in a sustainable way.