When COVID began to explode in March 2020, it became painfully clear the world didn’t have enough ventilators.
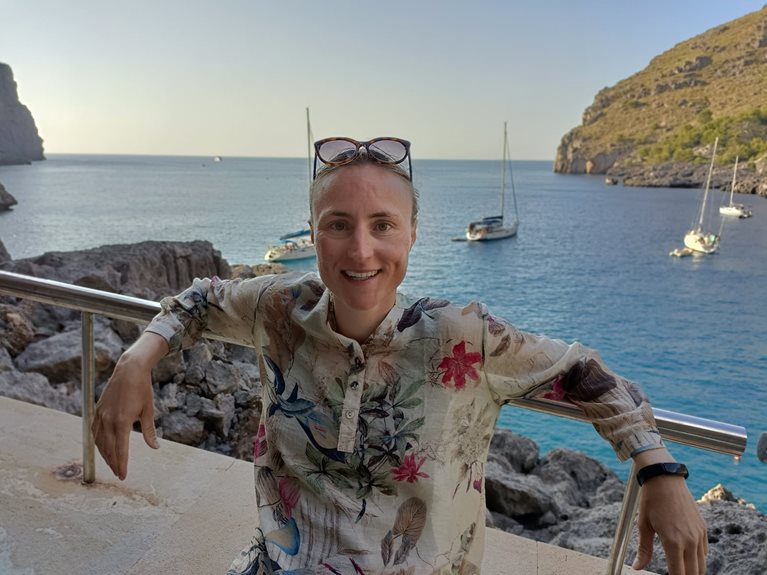
In my role as an Operations specialist at McKinsey, I joined a project team supporting Vyaire Medical, with the help of Spirit AeroSystems and specialized manufacturers, as it ramped up ventilator production to a pace not previously seen. At its peak, Vyaire was producing more ventilators in three days than it had in all of 2019 to try to keep pace with the surge in demand. It was an amazing accomplishment, driven by people devoted to such critical work.
For me personally, it was empowering to be doing something that would materially help make a difference during such a scary and uncertain time in our global history.
How I got involved in this once-in-a-lifetime project
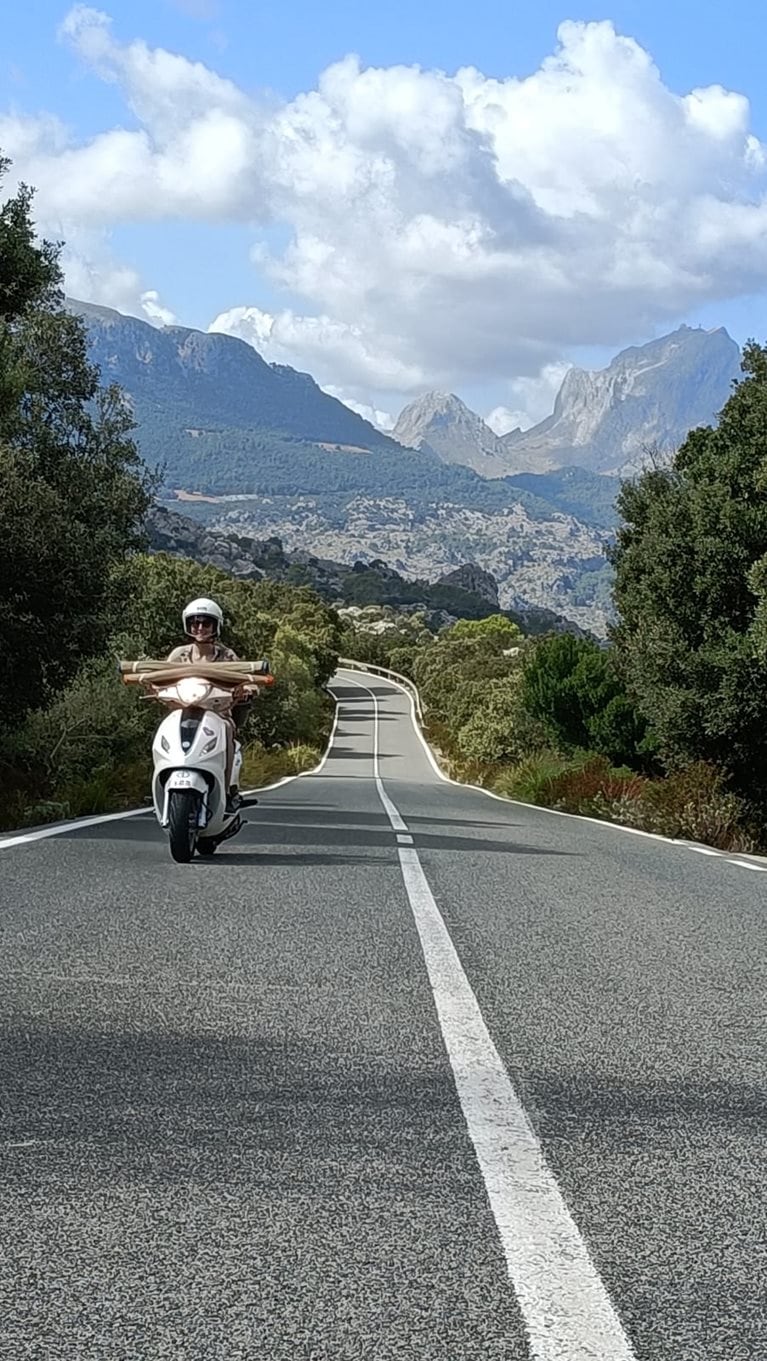
I studied industrial engineering and, after graduation, went to work for Porsche as a quality manager for engine components. I later came to McKinsey to widen my horizons by working on top management operations projects in different industries in various countries. I found the apprenticeship model offered within the Operations Excellence Program at McKinsey especially attractive since it seemed like a great opportunity to build a company-wide network.
During one of my first projects at the firm, I served a biopharma company. I enjoyed the work, clients, and colleagues so much that I started to move into that space more permanently. In the four years since, I have become dedicated to our Life Sciences practice.
As the pandemic began, I was involved in an internal project related to identifying potential substitutes for ventilator components that had become a bottleneck on the market and grew my expertise in the area. When McKinsey started serving Vyaire, I reached out to the McKinsey partners leading our team and raised my hand to join.
The outcome was a logistical feat
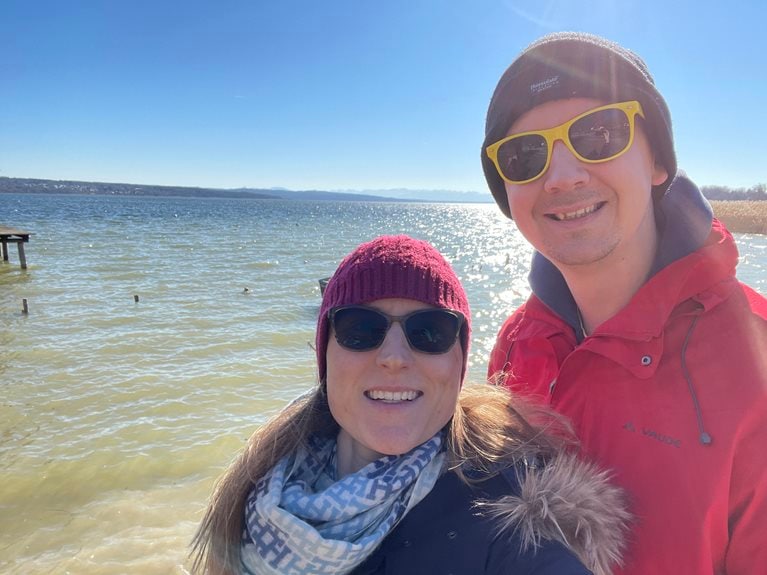
Our overall goal was to figure out how to help Vyaire scale ventilator production as quickly as possible given the surging need, without sacrificing quality. It required many moving parts. We had a US-based team working with Vyaire and Spirit AeroSystems to optimize a facility in Palm Springs and build a new facility in Kansas. We also had a team in Asia and Germany and colleagues supporting us from around the globe.
Supply chain issues added to the complexity of the work. Ventilators depend on many outsourced materials, so we worked with a wide array of globally dispersed suppliers that provide key components such as circuit boards, turbines, and displays. My team’s role to determine which components and suppliers were creating production bottlenecks and do everything we could to help the suppliers alleviate them. Every week, we tackled new challenges while looking ahead to predict issues which could arise in the future in hopes of preventing any slowdown in production. We also helped Vyaire and Spirit AeroSystems find new/additional vendors as necessary.
It all had to happen incredibly fast. At one point, we found a second source supplier that was able to retrofit a component into the ventilator within two months and get it ready for market including certifications and tests. That is incredible, when you think that it usually takes more than a year or two to get a certification for medical devices.
A master class in teamwork
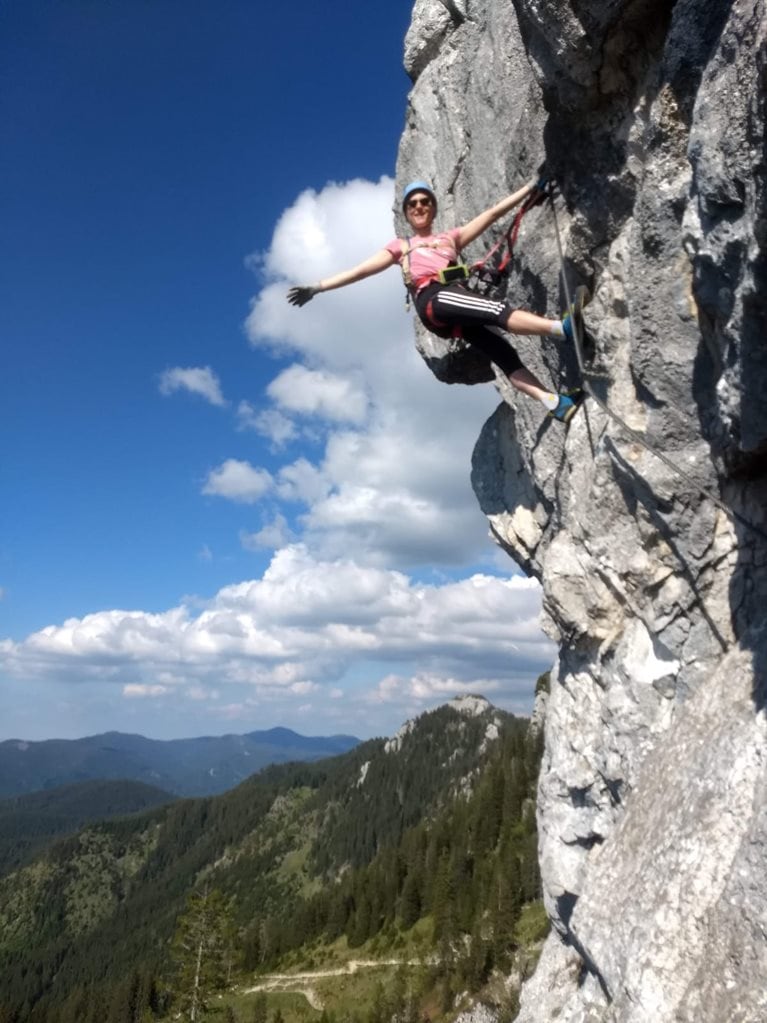
Without the rock-solid teamwork between Vyaire, Spirit AeroSystems and McKinsey colleagues, we couldn’t have done this. Engineers worked in shifts so they could work around the clock. Teammates in Malaysia repeatedly checked component inventory; others in the US spent days on the shop floor supporting manufacturing. Manufacturing experts installed sensors on production lines to pinpoint inefficiencies and increase output. At every turn, people came together and did what it took to support the cause.
Hard but meaningful work
I worked on this project for six months, my longest so far at the firm, and it was challenging and stressful. There were days when I would be in a 10 pm meeting with the US team, then an early-morning call with Asia the next day. It was worth it because I was helping healthcare communities combat the pandemic by doing the type of work I love to do. The challenges we faced helped me to grow my expertise and develop my skills, so I can better serve future clients, too.
More about Catherine
Catherine studied industrial engineering and received her master’s degree at Karlsruhe Institute of Technology (KIT). With a desire to focus on operations, she joined McKinsey’s Operations Excellence Program, which is a two-year program that helps you develop specialized expertise through apprenticeship and training in manufacturing & supply chain, product development & procurement, or service operations.