Recent events in the global economy mean many energy and materials companies are keen to reduce both operational and capital expenditures. As companies look to cut costs without hamstringing underlying businesses, they typically fall back on levers like back-office headcount reductions, procurement, and routine maintenance efficiency. These approaches can be quite successful when executed thoughtfully. But they can only yield so much value. As pressures continue to increase, new approaches are needed. One often-overlooked area of opportunity are shutdowns, turnarounds, and outages (STO).
For energy and materials players, outages typically consume between a third and half of the overall maintenance budget and can reduce annual production volume by 5 to 10 percent. Similar opportunities exist for major overhauls and equipment checks in travel, transportation and logistics companies - for example locomotive overhauls at railroads. Because turnarounds happen infrequently, typically last for a few weeks or more, and often include a mix of both operations and capital spend, many companies treat STO as something outside the normal course of business. As a result, STO often get less scrutiny and continuous improvement effort than "routine" activities.
Companies that manage turnarounds most successfully treat STO as part of a broader asset productivity picture. They look not just at costs, but also at overall asset reliability. They consider STO an investment in the plant, and hold operations, maintenance and engineering leaders accountable for delivering an acceptable return on investment through improvements in reliability, throughput, production cost, and quality. The teams managing STO events at top-performing companies aim to maximize the overall value of turnarounds by continuously optimizing across four areas: the cost of the turnaround event, the duration of lost production during the event, the reliability of the plant after the event, and the interval between events (Exhibit 1).
In our work on STO with dozens of energy and materials, and travel, transport and logistics companies over the past decade, we have identified six areas (Exhibit 2) where improved practices can deliver improvements in one or more of these core areas. Let's look at some examples of each.
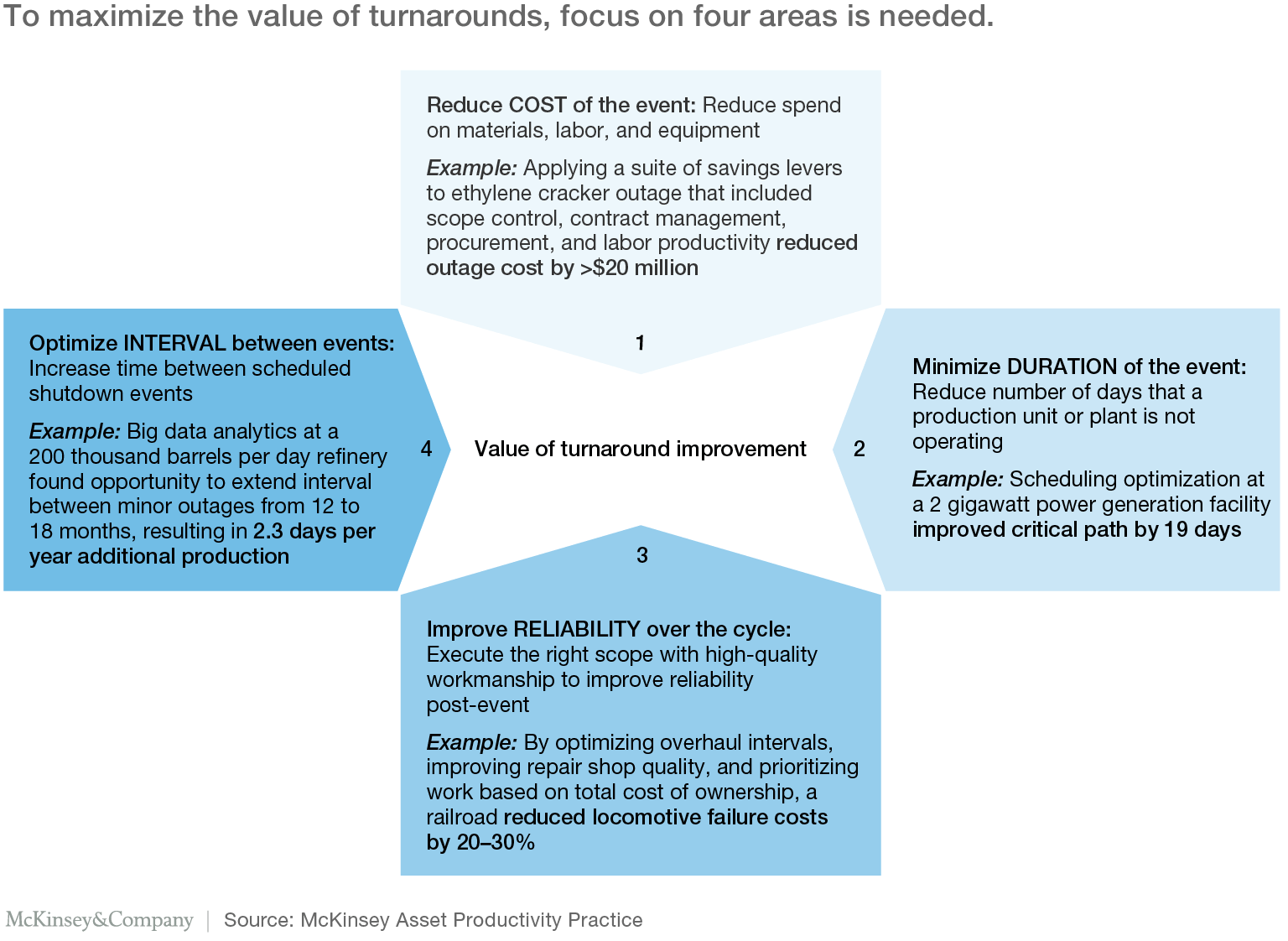

Strategic planning
Companies often base STO duration and cost targets on past performance, with a little added for inflation. In one example, successive turnaround management teams at a power company would add a 10 percent contingency buffer to the costs of previous events when setting the target for the next. As a result, turnaround cost had grown by nearly 50 percent over the last four events, while scope had remained essentially unchanged.
A better approach is to assess turnaround activities against best practices across industry sectors, and to aggressively challenge assumptions that may have long become corporate lore. The operators of one power generation plant, for example, wanted to reduce the duration of maintenance turnarounds from a historical average of 45 days to less than 30. The company ran a series of workshops, leveraging benchmarks and assessments for each major activity. Where risk or uncertainty was identified (e.g., major activities performed for the first time), a fact-based and risk-informed contingency was added for the specific job. With the new durations in hand, the company rebalanced activities between outages to level the scope and execution risk. As a result, the planned duration of outages was reduced to 26 days.
In another example, an oil refinery struggling to meet availability targets decided to reevaluate turnaround intervals at the plant. Working with site maintenance, operations, and engineering teams, managers modeled the plant and then used advanced analytical techniques to determine sources of unavailability, and to identify mitigations. Improvements included changing the preventive maintenance done during operations, upgrading critical equipment to more durable designs, and modification of operating procedures to extend service life. Using advanced analytical approaches, the company then modeled the impact of the changes to optimize tradeoffs in cost, reliability and outage interval. Applying these new measures, the company found it could extend the interval between week-long minor outages from 12 months to 18 months, increasing production by 2.3 days a year, equivalent to more than 500,000 bbl per year, with no additional risk to equipment failures or operating costs.
Scope development
The temptation in many companies is to "save up" maintenance and upgrade activities for the next scheduled turnaround. Thus, the scope of many turnarounds starts out too large, and scope "creep" during the planning phase is extensive.
To keep scope under control, leading companies establish a structured review process, with objective criteria to review the value, cost and risk associated with each proposed activity. Reviews are conducted by a cross-functional team to ensure alignment with a focus on potential cost reduction, as well as prioritizing the most important tasks consistent with desired equipment reliability.
For many organizations, one important shift in scope planning is the change from "challenge out" to "challenge in." Instead of assuming that an activity will be included in scope unless there is a good reason not to, this approach requires each activity to justify its own inclusion. This eliminates the problem that individuals are reluctant to take on the personal risk of denying a particular piece of work.
Finally, good practice requires an equally robust process to avoid unnecessary additions after the scope freeze date. Such a process should, for example, require rigorous review of the business rationale and sign-off by the STO Steering Committee for any proposed additions.
One oil and gas company adopted a new scope definition approach for STO planning in its downstream activities. After defining a set of scoping criteria, the company ran multiple post-STO workshops with operations, maintenance, engineering, and the turnaround organization to refine the scope for its next major turnaround. Using the above practices the company was able to reduce the overall work content of the planned event by 20 percent without deferring critical scope. The company expects to find further opportunities as it uses this experience to inform the planning of future events.
Planning and scheduling
All that many companies ask of their turnaround schedule is that the event be completed on time. Unfortunately, this approach can encourage managers to include multiple layers of contingency, with little incentive to actively minimize schedule risks or optimize shutdown duration.
Leading companies make the financial impact of lost production a top focus for management, and turnaround teams make extensive use of lean techniques to improve speed and productivity during turnaround events. Training turnaround planning teams in the use of lean tools like Single Minute Exchange of Dies (SMED) and schedule optimization techniques can drive dramatic improvements over time. One leading company's turnaround team held a day-long session devoted to optimizing the schedule for an STO event and finding ways to reduce the scheduled critical path by more than 20 percent.
Companies can also make rapid short-term improvements simply by developing a database of known best-practice time saving approaches. Example practices include streamlining the permitting process, and choreographing the handover between operations and maintenance teams during shutdown and restart activities. When one chemical company tapped into a best-practice improvement database in the months leading up to a planned 24-day turnaround event, it was able to find opportunities to reduce duration by three days.
Preparation and execution
Turnarounds are large, complex, compressed events. Just as great sports teams rarely win games by making up their tactics on the fly, effective preparation and disciplined execution are critical to a successful outcome.
Best practices in turnaround preparation focus on understanding the most important risks in advance and developing detailed contingency plans. Identifying and mitigating risks typically requires a cross-functional assessment prior to the event. Addressing risks prior to the outage is much less costly than firefighting during the event. For example, if disruption from bad weather is a significant threat to an activity on the critical path, it might be worth erecting a cover over the work site. "Normal" activities that frequently contribute to delays or disruption, like complex "lock-out, tag-out" protocols or demanding regulatory requirements, can also be tackled in the risk management process. The turnaround team can then create detailed plans up front to address them.
During turnaround execution, progress against the schedule, especially the critical path, should be updated daily and made visible to all stakeholders, so potential issues can be addressed as soon as they occur. The execution of work that is not on the critical path should also be monitored closely, because, if progress slips, such jobs can get pushed onto the critical path and produce delays.
Placing dedicated teams against each element of outage preparation and execution, including emergent issue management, has been shown to consistently improve performance. Top-performing companies have also found it useful to manage turnaround preparation and execution using regular "War Room" meetings held in a dedicated space with visual displays of critical information such as outage context, performance metrics, schedule updates, and cross-functional enablers (Exhibit 3). Putting information and decision-makers together in one place ensures everyone has the same picture of turnaround progress, and enables faster, fact-based decision-making when issues emerge.

Contractor and vendor management
To meet tight timelines, turnarounds typically require substantial contractor resources. Managing those contractors is therefore a critical element in turnaround success.
Best-practice companies ensure contract terms are tight. They identify opportunities within contracts to reduce demand or improve execution efficiency and determine the terms and conditions that need to be closely managed. Furthermore, they involve contractors early in the planning process to ensure everyone understands the scope of the turnaround and their responsibilities. This also allows contractors to suggest ideas for schedule optimization or productivity improvements, and to get familiar with the assets where they will be working. During execution, best-practice companies track contractor performance closely against the contract terms; for example, they verify the work completed on a per-unit basis, or track manpower on site if the owner is paying for time and materials.
Management systems and governance
Because STOs happen infrequently, management teams—both those leading the turnaround and overall site leadership teams—often change significantly between events. This makes it difficult for companies to apply the learning from one event to the next. Turnarounds also involve multiple stakeholders. These groups may have competing interests that are difficult to reconcile. Finally, many organizations delegate the responsibility for turnaround events to mid-level managers, who may lack the experience or influence to push for optimal outcomes.
To minimize these issues, the best companies take a highly systematic approach to the management of turnarounds. They identify the processes, capabilities, and resources they need for all aspects of the turnaround. Before each turnaround event, they conduct a review to ensure all these elements are in place and carry out training where necessary to fill any gaps.
Strong companies are equally systematic about immediately capturing the learning from each turnaround they do. They may, for example, establish a cross-functional team to review the actions taken in each event, identify issues and possible improvements, and share that knowledge for future use.
* * *
STOs can be intimidating events to optimize as they couple the complexity of building a major capital project with the risk of working in an existing plant, all compressed into a brief window of time. Many companies avoid the challenge of improving STO. But for those willing to take a closer look, the opportunity can be substantial, with schedule and cost improvements of 10 to 30 percent not uncommon.
About the authors: Matt Gentzel is an associate partner in McKinsey’s Pittsburgh office, where Alan Osan is a master expert; Bill Lacivita in an associate partner in the Atlanta office, and John Parsons is a partner in the Calgary office.