Every step of semiconductor manufacturing, from wafer manufacturing through packaging, requires fossil fuels and generates emissions. To address climate change, some semiconductor companies have recently taken major steps to decarbonize. These efforts are the first steps in the transition to more sustainable operations, and they are intensifying as the companies’ major end customers establish even more ambitious emissions reduction targets. Intel, for instance, recently committed to net-zero greenhouse-gas (GHG) emissions in its global operations by 2040 and has targeted achieving 100 percent use of renewable electricity as an interim milestone in 2030. Since semiconductor companies are often among the suppliers with the greatest emissions, they will face particular scrutiny as end customers increasingly look upstream.
As semiconductor companies race to meet supplier expectations, they must broaden their decarbonization efforts. To date, most of their programs have focused on two emissions categories: those directly related to activities within their fabs (Scope 1) and those arising from the generation of purchased electricity, steam, heating, and cooling equipment (Scope 2). Since Scope 1 and 2 emissions represent only 65 percent of total GHGs from fabs, companies can only meet their customers’ net-zero goals by expanding their efforts to include Scope 3 upstream emissions—those originating from the suppliers that provide services or silicon and other materials for chip manufacturing.1
Many semiconductor companies have hesitated to address Scope 3 upstream emissions because of the challenges encountered to date when attempting to create transparency about emissions and drive decarbonization initiatives. The problems largely arise because emissions are fragmented across hundreds of suppliers and thousands of materials. But semiconductor companies may now overcome these hurdles by applying new methodologies, leveraging automated baselining tools, and driving their Scope 3 upstream decarbonization in cross-functional programs that have top management support. In this article, we explore the way semiconductor players can decarbonize their Scope 3 upstream emissions by facilitating cooperative efforts with suppliers, improving waste management, redesigning or enhancing product specifications, and optimizing use of materials.
Scope 3 upstream emissions: An overlooked but important category
Our analysis suggests that upstream emissions for a typical fab have three main sources (Exhibit 1):
- purchased materials (representing about 62 percent of all Scope 3 upstream emissions)
- maintenance services, spare parts, and capital expenditures for equipment upgrades (about 22 percent)
- supplier transportation, such as material deliveries (about 6 percent)
Of course, every fab may differ from the norm in some respects. For instance, some companies may already rely on chemical suppliers that prioritize renewable energy. But one factor common to many fabs is a lack of clarity about Scope 3 upstream emissions, including the amount associated with specific materials, services, or suppliers. For example, nitrogen trifluoride (NF3), which is commonly used in semiconductor fabrication, rates very high for global warming potential. Fugitive emissions—those that escape unintentionally—related to the production of NF3 may be higher than the emissions associated with the actual NF3 production process, but these are very difficult to quantify.
Many semiconductor companies may also use misleading assumptions to calculate their Scope 3 upstream emissions. Consider aluminum. While most industries can use 99 percent pure aluminum with no complications, semiconductor companies often require 99.9 percent purity—and that slight improvement requires far more energy, partly because of repetitive melting and cooling as well as the electrochemical purification required, which increases the emissions. The same pattern holds true for many other materials.
While fabs may deal with hundreds of suppliers during procurement, our analysis revealed that about six to ten suppliers will account for half of emissions for chemicals, wafers, and gases (Exhibit 2). For maintenance, spare parts, and capital expenditures for equipment upgrades, about three to five suppliers will account for over half of emissions. These patterns mean that semiconductor companies can address the majority of Scope 3 upstream emissions by focusing on a relatively small group of suppliers.
The first step in decarbonizing Scope 3 upstream emissions involves establishing a detailed and reliable baseline. This can be done by examining procurement data for Tier 1 suppliers, including the exact quantities of materials purchased. While fabs will ideally base their analysis on volume data whenever possible, this information may be unavailable or irrelevant for some categories, such as services. In such cases, they must examine spending levels instead. When estimating emissions associated with different materials and services, our approach calls for fabs to factor in the high-energy requirements needed to create semiconductor-grade quality materials (for more information, see sidebar “Our methodology for estimating Scope 3 upstream emissions”).
Finding the right decarbonization pathways for Scope 3 upstream emissions
Once semiconductor companies have established emissions baselines for Tier 1 suppliers, they must identify the right set of decarbonization levers to reduce their emissions, focusing on the suppliers and materials that contribute most emissions. The full range of levers spans four areas and requires the involvement of different stakeholders in the organization (Exhibit 3). Semiconductor companies should consider all of these levers to develop the most effective and efficient approach to decarbonization.
Some gains may come from requiring suppliers to use renewable materials or from identifying ways to reduce waste within fabs, thereby decreasing the volume of materials ordered. Other levers involve optimizing the materials used (for instance, using metals with a lower emission footprint or changing product specifications to reduce the need for high-emissions materials). Fabs should consider the cost and decarbonization potential of all levers, but their ability to implement them will differ. The internal stakeholders or functions involved will also vary.
Top leadership commitment and involvement is essential to drive decarbonization across the different functions, including operations, technology, development, and procurement.
Supplier decarbonization
When helping suppliers decarbonize, fabs may want to focus on the top three materials categories—chemicals, wafers, and gas—because of their outsize impact on Scope 3 upstream emissions.
In many cases, fabs may be able to reduce emissions by switching from their current Tier 1 suppliers to those with lower carbon footprints. But if they want to preserve their existing relationships or have no alternatives, fabs can cooperate with their current suppliers to accelerate decarbonization programs. For instance, they might jointly agree on emissions reduction targets, identify abatement levers, and define execution road maps.
Would you like to learn more about our Semiconductors Practice?
For many purchased materials, including wafers, hydrogen peroxide, nitrogen fluoride, and aluminum, energy from conventional sources will account for more than half of emissions during production. Fabs might be able to reduce this percentage by offering financial incentives or other benefits to encourage suppliers to increase their use of renewable energy. The ability to apply this lever will vary, however, since suppliers may be located in countries that offer limited access to renewable energy. For some chemicals and process gases, fabs might also collaborate with suppliers that can offer innovative production processes or synthetic routes that lower overall emissions.
Many emissions arise from Tier 2 suppliers that do not interact directly with fabs, or from suppliers that are even further upstream. These suppliers also contribute to a fab’s Scope 3 upstream emissions, so they need to be part of any decarbonization efforts. Tier 1 suppliers might be best positioned to encourage Tier 2 suppliers to reduce emissions, since their relationship as end customers may give them more leverage. While it may seem difficult for suppliers to cooperate along the value chain, examples of past collaborations exist. For instance, semiconductor companies and Tier 1 suppliers of tools and chemicals worked closely together to reduce the usage of perfluorocarbons when regulators began discouraging their use.
Although semiconductor companies deal with too many suppliers to develop an individual decarbonization plan for each one, they can still drive improvement throughout the entire vendor base by implementing new procurement strategies, such as policies that give preference to suppliers that disclose their emissions or that have lower emissions than their competitors (see sidebar “Decarbonizing wafer production” for examples of concrete steps that fabs can take).
Waste reduction
Over the short to medium term, fabs can also reduce Scope 3 upstream emissions by taking steps to decrease waste within their facilities, but they must first balance trade-offs and identify potential risks. Consider wafer cleaning. A single wafer runs through more than 100 different chemical baths while being processed. Fabs might be able to increase the number of wafers processed in the same chemical bath to reduce waste, but cross-functional teams would first need to determine when reuse might decrease yield to an unacceptable level. Fabs might also investigate whether they can extend the life of machine parts by increasing predictive maintenance, or determine if they can reduce use of spare parts by specifying that they should only be replaced once specific triggers, such as particle counts, are exceeded.
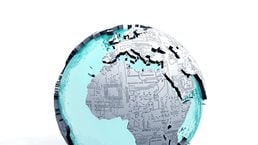
Keeping the semiconductor industry on the path to net zero
Recycling—an area where few fabs undertake extensive efforts—could also decrease waste if leaders expand their current programs. For instance, they could investigate the possibility of introducing recycling programs for materials, such as ultra-high-purity aluminum, that have not been previously reused. Whenever recyclates are investigated, fabs must determine how they can remove impurities to meet the semiconductor industry’s high standards. Moving recycling on-site could also decrease waste.
Materials optimization
In some cases, fabs may be able to use lower-emissions materials, chemicals, or gases during production. First, however, companies must set up R&D, quality, and engineering teams to identify better manufacturing methods, evaluate alternatives, and review product specifications. With any change in production or composition, the teams must evaluate trade-offs, such as a potential decrease in product performance, and determine what is acceptable.
To facilitate progress, semiconductor leaders may cooperate with industry organizations to develop green alternatives to emissions-heavy materials, chemicals, and gases, such as fluorinated chemicals.
Product-specification adjustments
Fabs might contemplate changing product specifications to reduce emissions—for instance, they could evaluate whether existing purity grades for certain metals are truly essential. Again, many trade-offs come into play. In some cases, loosening requirements may achieve the dual goal of reducing emissions and driving cost improvements. In other instances, however, less stringent requirements might introduce quality issues that lower yield.
Since fabs have not made any extensive efforts to reduce emissions by changing product specifications, their initial focus should involve fairly straightforward solutions, such as the use of lower-grade chemicals during less critical steps of the wafer-cleaning process. Over the longer term, they can consider more complex process changes, such as finding replacements for highly emissive materials, since these may become increasingly important as semiconductor end customers push for zero emissions throughout the supply chain.
Although the supplier landscape is fragmented, with many vendors and products, companies can still develop a viable strategy for reducing Scope 3 upstream emissions. With six to ten suppliers accounting for half of all emissions for chemicals, wafers, and gases—the top three materials categories—fabs may want to concentrate their initial efforts on this group. When implementing decarbonization levers, the effort must go beyond procurement to encompass product and operational changes. Such broad efforts may actually produce better results, since many semiconductor companies encounter difficulties when attempting to change suppliers. Because decarbonization efforts will be broad in scope, they will require the involvement of top leadership and stakeholders from all relevant groups, including operations, procurement, and R&D. Some semiconductor companies are already launching initiatives to reduce Scope 3 upstream emissions, and they could emerge as early leaders. Now it’s time for others to follow their example.